Towards Human-Robot Co-Agency
Project subtitle: AI and Feminist Technoscience Perspectives for Diversity, Demography, and Democracy in Human-Robot-Collaboration in Architecture
Abstract
Robotic arms are promising tools for the fabrication and construction industry for their mobility, multi-action capacity, durability, and sustainability. Collaborative robots (cobots) and Human-Robot Collaboration (HRC) provide a solution to bridging the skill gap, retaining skilled staff, and attracting the younger generation [9], in addition to improved productivity, efficiency, quality, and worker safety. However, the lack of qualified workers and robots’ limited response to uncertainties hinders their adoption in fabrication and construction environments. There is a demand for human-centric human-robot collaboration design approaches that are (1) inclusive to both skilled workers and novices, (2) replace demands for human physical labor with demands for intellectual skills, (3) alleviate coding difficulties, (4) engage workers meaningfully by stimulating creativity and ensuring agency, and (5) improve robots response to uncertainties to better collaborate with humans. Deep Reinforcement Learning in simulated and real-life training can potentially increase robots' autonomy and response to uncertainty. This dissertation proposal integrates perspectives from Feminist Technoscience, a transdisciplinary field offering distinct ways of thinking about societies and their needs when designing technologies, to develop a Human-Robot Collaboration method that attracts skilled staff, includes varied demographics, supports skills, and decision-making. The method comprises robotic arms’ pre-training with Deep Reinforcement Learning to improve uncertainty responseability and better collaborate with humans. The method development process will include user studies, testing the engagement and satisfaction of a diverse set of potential users varying in age, gender, and proficiency levels.
- Relevance of the Topic
New approaches in design and fabrication are urgently required to (1) meet the challenges of rapid urbanization and population growth, (2) increase the productivity of the stagnated building sector, suffering from time and budget overrun, and (3) reduce resource and energy consumption and carbon footprint. The Cluster of Excellence Integrative Computational Design and Construction for Architecture (IntCDC) at the University of Stuttgart aims to harness the full potential of digital technologies to rethink design, fabrication, and construction in the building sector. This dissertation proposal relates to this mission with a novel method for HRC that is approached from a human-centric perspective and seeks to engage broader and more diverse demographics meaningfully. HRC is increasingly important due to its relevance in addressing skill shortages in the architecture and construction industry with digital fabrication in the factory and on-site. In the context of IntCDC research,
IntCDC develops a robotic platform for timber fabrication that consists of two industrial robots (RP4: “Cyber-Physical Wood Fabrication Platform”; RP9: “Data Processing and AI for Predictive and Adaptive Co-Design in Prefabrication and On-Site Construction”), but the integration of this platform into the timber construction industry remains challenging. This proposal aims to combine human and machine intelligence to improve the integration of robotic fabrication platforms into the construction industry by (1) developing novel collaborative fabrication processes, (2) developing a novel HRC method to improve engagement for broader audiences, and (3) improving interface design to support a variety of cognitive contributions. While the dissertation is in digital design and fabrication, its innovative design for a novel HRC method transcends this context. The project is relevant for a diverse participation in technological endeavors in general.
- State of the Art
The urgent need to enhance sustainability, productivity, and growth [1-6], as well as to solve employee shortage [7] and promote worker’s safety [8] in the fabrication and construction industry highlights the keen attention and investment directed towards advancing automated fabrication, and specifically the use of robotic-arms [9, 10]. Robotic arms are promising tools for their mobility, multi-action capacity, durability, and sustainability [11,12]. However, skilled workers’ scarcity and robotic arms’ limited ability to handle uncertainties impede their integration in fabrication and construction environments [13]. Collaborative robots (“cobots”) and Human-Robot Collaboration processes (HRC) provide a solution to bridging the skill gap, retaining skilled staff, and attracting the younger generation [14], in addition to improving productivity, efficiency, quality, worker safety, and reducing worker’s workload [15]. Previous research in HRC in building methodologies uses responsive, digital design-to-fabrication-workflows [16-19] to augment human capabilities in design, fabrication, and assembly, increase tech-accessibility with interactive interfaces, and provide live updates to the users and the system with sensing technologies and digital display. However, introducing gear-heavy and code-based processes into architectural fabrication and assembly further limits potential users [14]. Current challenges in HRC design are to (a) increase autonomy in robots (providing timely responses to deficiencies and change) for improved performance in HRC, (b) shift from gear-intensive processes to easy access interfaces, (c) include varied demographics for their meaningful contribution in HRC.
(a) Deep Reinforcement Learning (RL) algorithms train cobots’ autonomous performance in both digital and physical environments, supported by sensors and cameras [20]. Unlike explicit coding, RL rewards adaptive behaviors [21], thus improving robots’ ability to adapt to changes in that environment [22, 23]. Studies in RL for cobots’ autonomous assembly train for uncertainties such as part-positions, slippage in gripping, assembly towards a desired configuration [24, 25], and multi-step planning [26, 27]. It shows potential in tasks that can be transferred to the real world [21-28].
(b) Haptic teaching is a code-free method that allows users to control cobots directly through physical demonstration. It registers human gestures with force-torque sensors on the cobots’ joints, recording paths as points or a continuum. Haptic teaching is studied for accurate timber joint assembly and incorporated into RL with states [26, 28], and Zero-shot demonstration [29].
(c) Increasing participation of different age groups, backgrounds, and genders can be achieved with a focus shift from physical to cognitive contributions, meaningful worker participation, and accessible interface for users with varied technological backgrounds [16-18].
(c) Feminist Technoscience critique (FTS) is a transdisciplinary field offering a critical view of society, technologies, and the environment, proposing new viewpoints on agencies of humans and non-humans [30-35]. FTS highlights the definition and roles of agents and agencies, their co-effects, enhancements, responses, and responsibilities [34, 36-39]. Related to HRC design, FTS critique is essential in improving users’ engagement with technological developments [34, 40-49], inclusive design [41-44], promoting designs that are based on users’ needs [42-48], and tackling issues of trust with technology [40-49].
- Research aim
This proposal aims to combine human and machine intelligences to improve the integration of robotic fabrication into the construction industry by (1) increasing autonomy in robots, for improved co-agency with humans, (2) developing a novel HRC method to improve engagement for broader audiences, and (3) improving interface design to support a variety of cognitive contributions. These challenges will be investigated by exploring co-design of AI-supported robotic fabrication: RL and FTS critique for a meaningful engagement of broader workforce demographics. The guiding assumption is RL’s efficiency in finding dynamic policies combined with human capabilities in creativity, improvisation, and professional experience can provide an adaptable and responsive approach to uncertainty in construction.
Research questions:
- Inhowfar does AI-supported robotic fabrication support a successful performance in human-robot collaboration in construction?
- Inhowfar does FTS critique and AI-supported robotic fabrication engage diverse demographics, ensuring their agency, feeling safety and trust, in human-robot collaboration in construction?
- Inhowfar can AI for increased autonomy in cobots support an HRC under uncertainty and support human meaningful participation in construction?
- Inhowfar does human feedback improve AI for responsive HRC under uncertainty in construction?
- Inhowfar does a haptic-supported interface introduce new and diverse demographics in human-robot collaboration in construction?
- Methodology
The research questions are investigated through experiments in which computational design and RL-supported robotic fabrication are employed in empirical data acquisition in collaborative fabrication and assembly tasks. The RL training includes simulated RL in Unity with ML-Agents, Tensor Board, and AI Gym, and real-life RL with a NEURA LARA8 collaborative robot (“cobot”) equipped with a gripper, a depth camera, and a force torque sensor. The experiments involve user studies where a diverse demographic performs collaborative timber assembly tasks of similar, small-scale units with cobots. HRC task performance will be evaluated by (1) the height of the assembled tower - signifying an accurate pick and place; (2) the speed of turns turning- a signifier for a successful collaboration and humans’ trust in the cobot; (3) user feedback. A user questionnaire designed in collaboration with the Institute for Social Sciences (SOWI), University of Stuttgart, will note users' impressions of HRC design and their feelings of safety and trust. The study will take place at the IntCDC LCRL Lab, Waiblingen.
Q1 will be answered with a small scale HRC demonstrator: testing a successful collaboration of participants and a cobot pre-trained with RL.
Q2 will be answered by a small-scale HRC demonstrator, who will test a diverse demographics’ response to cobots, either point-to-point programmed or pre-trained with RL.
Q3 will be answered by a small-scale HRC demonstrator, testing a successful assembly by participants and a cobot pre-trained with RL, where the cobot responds live to human behavior previously unknown.
Q4 will be answered with a small-scale HRC demonstrator: testing a successful assembly by diverse demographics and a cobot pre-trained with RL, where participants are asked to propose solutions to uncertainty and further guide a cobot with a haptic demonstration.
Q5 will be answered by a small-scale HRC demonstrator, who will test a diverse demographics' response to a collaborative process with a cobot pre-trained with RL, including a haptic demonstration.
While the project’s demonstrator explores close collaboration with AI-supported cobots, its innovative design for a novel HRC method transcends this context: the project is relevant for diverse participation in technological endeavors in general.
- Expected results
This doctoral research will develop a novel Human-Robot Collaboration (HRC) method based on deep reinforcement learning, novel reward functions (RL), and user feedback to optimize fabrication and assembly processes for (1) increased autonomy and improved integration of robots, (2) improved performance seen in response to deficiencies and (3) inclusion of new demographics in HRC. In redesigning human-robotic agency, the efficiency and inclusivity of such collaborations can increase: increasing robots’ autonomy with RL, allowing timely responses to deficiencies with human feedback, and introducing new users for their intellectual contribution (and not physical). A series of demonstrators will realize the feasibility of these proposals. The results will be published in 3 journal publications, detailed in Annex-1.
PROJECT TEAM
Institute for Computational Design and Construction (ICD), Department for Computing in Architecture (CA) University of Stuttgart; The International Max Planck Research School for Intelligent Systems (IMPRS-IS).
Gili Ron, Prof. T. Wortmann, Prof. A. Menges
PROJECT FUNDING
Stuttgart Research Focus “Interchange Forum for Reflection on Intelligent Systems (IRIS), funded by the Ministry of Science, Research and the Arts of Baden-Württemberg Az. 33-7533-9-19/54/5
Cluster of Excellence Integrative Computational Design and Construction for Architecture (IntCDC) (EXC 2120/1 RP4)
RELATED PUBLICATIONS
Ron, G., Menges, A. & Wortmann, T. (2024). "Critical Collaboration: Reflecting on Power and Agency in Human-Robot-Collaboration in Architecture and Construction, for a Diverse and Democratic Practice". In: P. Eversmann, C. Gengnagel, J. Lienhard, M. Ramsgaard Thomsen & J. Wurm (eds.), DESIGN MODELLING SYMPOSIUM KASSEL 2024 – SCALABLE DISRUPTORS (re)new(able) materials and circular design and construction processes (p./pp. 191–204), August, Springer. ISBN: 978-3-031-68274-2. https://doi.org/10.1007/978-3-031-68275-9_16
Ron, G., Wortmann, T., Kropp, C. & Menges, A. (2025). "Human-Robot Reconfigurations: Advancing Feminist Technoscience Perspectives for Human-Robot-Collaboration in Architecture and Construction". In: M. Kanaani (ed.), The Routledge Companion to Smart Design Thinking in Architecture & Urbanism Fora Sustainable, Living Planet (pp. 669-679) . Routledge, Taylor & Francis Group. ISBN: 978-1-032-46990-4. DOI: https://doi.org/10.4324/9781003384113
Contact information
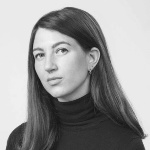
Gili Ron
M. Arch, B. ArchResearch Associate, Ph.D Candidate