Programming Shape-change
Integrative computational design of materials, mesostructures, and motion mechanisms for 4D printing
Shape-changing material systems are advantageous as passively actuated mechanisms for generating movement, with applications ranging from weather-responsive architectural building skins to self-shaping manufacturing of building components. 4D printing, a technique combining stimuli-responsive materials with additive manufacturing, is a promising method for the fabrication and physical programming of shape-changing structures. However, limitations in material responsiveness, programmability of shape change, and robustness of structures have limited their functionality and real-world applicability. This dissertation introduces an integrative computational fabrication approach for the development of 4D printed hygroscopic material systems based on co-designing materials, mesostructures, and motion mechanisms. By tuning the material properties and structuring in hierarchical length scales, highly functional and precisely programmable 4D printed material systems have been developed. This material programming approach has been demonstrated through three studies, each focusing on one of the abovementioned aspects:
- By co-designing biobased cellulose-filled materials for 4D printing, the responsiveness of structures to target ranges of ambient relative humidity levels has been tuned.
- By precisely designing the mesoscale material structuring inside the 4D printed elements, their spatial and temporal shape-change have been programmed.
- And through the development and utilization of computational fabrication workflows for 4D printing, novel motion mechanisms with enhanced functionality, such as motion amplification, have been created.
The proposed material programming methodology and the developed material system have been implemented in the design and fabrication of the SolarGate, a 4D printed, weather responsive façade system installed on the LivMatS Biomimetic Shell. Comprised of 424 4D printed shading elements, the SolarGate regulates the solar heat gain of the building by providing adaptive shading in response to daily and seasonal weather cycles without consuming any operational energy. These results showcase the potential for creating an architecture that is highly functional, ecological, and in tune with the environment, being powered by and at the same time empowering the earth.
PROJECT TEAM
ICD Institute for Computational Design and Construction, University of Stuttgart
Yasaman Tahouni, Prof. Achim Menges
PROJECT FUNDING
German Federal Ministry of Food and Agriculture within the framework program Renewable Resources (FNR) (22018116)
State Ministry of Baden-Wuerttemberg for Sciences, Research and Arts (MWK) (33-7533.-30-121/15/3)
Deutsche Forschungsgemeinschaft (DFG, German Research Foundation) under Germany’s Excellence Strategy – EXC 2120/1–390831618 (FIT_Bridge)
University of Stuttgart, Wissens- und Technologietransfer (WTT) (ZeroFassade)
RELATED PUBLICATIONS
Tahouni, Y., Cheng, T., Lajewski, S., Benz, J., Bonten, C., Wood, D. and Menges, A., 2023. Codesign of Biobased Cellulose Filled Filaments and Mesostructures for 4D Printing Humidity Responsive Smart Structures. 3D Printing and Additive Manufacturing, 10(1), pp.1-14. DOI: 10.1089/3dp.2022.0061
Tahouni, Y., Krüger, F., Poppinga, S., Wood, D., Pfaff, M., Rühe, J., Speck, T. and Menges, A., 2021. Programming sequential motion steps in 4D-printed hygromorphs by architected mesostructure and differential hygro-responsiveness. Bioinspiration & Biomimetics. DOI: 10.1088/1748-3190/ac0c8e
Krüger, F., Thierer, R., Tahouni, Y., Sachse, R., Wood, D., Menges, A., ... & Rühe, J., 2021. Development of a material design space for 4D-printed bio-inspired hygroscopically actuated bilayer structures with unequal effective layer widths. Biomimetics, 6(4), 58. DOI: 10.3390/biomimetics6040058
Tahouni, Y., Cheng, T., Wood, D., Sachse, R., Thierer, R., Bischoff, M. and Menges, A., 2020. Self-shaping Curved Folding: A 4D-printing method for fabrication of self-folding curved crease structures. In Symposium on Computational Fabrication (pp. 1-11). DOI: 10.1145/3424630.3425416
Contact Information
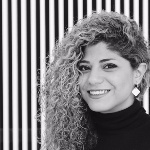
Yasaman Tahouni
S.M.ArchS, M.Sc.Research Associate, Doctoral Candidate